FAQ
The list below are some of the commonly asked hole punching questions with answers from our experienced staff at Unittool Products. Our business is to provide you with high quality hole punching systems and the knowledge to operate and maintain your tooling.
We invite you to contribute to this section by sending your questions to info@unittool.com. Your input and suggestions are greatly appreciated.
A: Too much clearance will create a burr which may not be acceptable. If the clearance is too tight the process will require more tonnage, the punch and die will wear out prematurely, and it will require more force to strip the punch from the material.
A: There are several reasons for this condition. First, dull punches will cause the material to improperly fracture the material. This is evident by checking the burnished area on the slugs. This burnished area should be approximately 20 percent of the total material thickness.
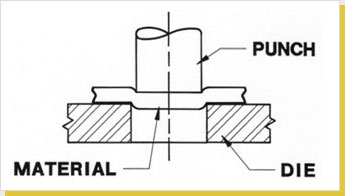
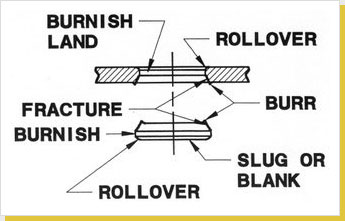
Second, stripping springs that are worn and have taken a set will not provide full stripping pressure. The specifications for new spring lengths are listed on the catalog page for each unit. This combination of dull punches & dies and fatigued springs results in the reduced tooling performance. As a general rule, we recommend to sharpen often and take light cuts.
A: As an example, let’s say you need to punch .875″ diameter holes in 3/16″ type 304 Stainless. The formula begins the same as for mild steel:
3.1416 x .875 (Dia. Of Hole) x .187 (Mat’l Thickness) x 25 = 12.8 Tons for mild steel
Because stainless steel has a higher shear strength, a multiplier factor of 1.40 is required.
12.8 (Tons for MS) x 1.4 (Multiplier for stainless) = 17.9 Ton per hole required.
A: The basic rule is to keep the upper arm components of Unittool tooling well lubricated and the frequency varies from each press environment. An inspection of the moving components is recommended during and after a normal shift. Some materials such as hot rolled steel or galvanized steel that create scale when punched will require additional maintenance. For daily operations, we recommend light machine oil – SAE 10 or equivalent. Lubricants that contain chemical driers are not recommended.
A: To prevent your part from distorting at the hole locations, Unittool recommends that the punched hole be located a minimum of 1½ to 2 times material thickness from the edge of the hole. The diagram shown here depicts what can be avoided when adhering to these guidelines.
A: This is the actual dimension added to the punch dimension based upon the type and material thickness of the material being punched. For Unittool tooling, we refer to this as Total Die Clearance.
A: Example: You need to punch a 7/8” diameter hole in 10 gauge mild steel. Convert the material gauge into decimals. 10 gauge steel = .1345”. Multiply .1345” X 20%. Answer = .027”. Add this to the punch size. Punch .8750” + .027” = .902” Total. The die size equals .902”.
A: The total height from the base of the Unittool holder to the top of the punch, with the unit in the normal closed position. See unit pages for individual operating specifications.
A: This is the measurable force that is required for punching and notching material.
A: First, you need to obtain the press specifications by locating the model number. Once you have determined the press tonnage, a guideline of 65% of the press tonnage is typically used for hole punching and notching applications. Example: You have a 50 ton press. Multiply 50 tons X 65% = 32 ½ Tons Available for Punching. (Note: this percentage may change based upon the age and condition of the press equipment)
A: A series of punching units, part gauges and mounting components that when assembled becomes a flexible system to produce parts. Tooling and gauges can be repositioned as required. Unittool modular press tooling is available for heavy, medium and light gauge part producing applications.
A: Yes. Multiple operations are easily combined to eliminate separate processes. With the Unittool modular system, you can punch, notch, shear, form and blank complete parts with each press stroke.
Have our experienced team review your specific application. We can help determine the best solution to produce your parts faster.
- Type of parts – e.g. Structural, Formed, Flat or Extrusion
- Type of material – Steel, Aluminum, Copper, etc.
- Material Thickness
The Unittool H-Series will punch heavy material up to ¾” thick. The M-series will punch up to 10 gauge mild steel and the L-series is designed for lighter gauge applications in both flat and formed parts.
A: The Unittool tooling system will operate in most down acting press brakes or punch presses. The types of parts that you will produce and the material thickness are the deciding factors in determining press designs. Contact the Unittool sales and engineering department for further assistance.
The orientation of the shape is the position of the shape in relation to the front of the punching unit.
For example, when ordering an obround punch, select whether Point X is at the front of the unit or the side of the unit, as shown below:
Point X at front of unit
Point X at side of unit
The guide has two slots at 0 and 90 degrees. The pin in the punch fits into one of these slots to orient the shape. Regardless of how you order the orientation of the shape (Point X at front of unit or Point X at side of unit), you can utilize either position.
Returns
Unittool offers a 30 day return policy on stock items and standard size punches.
Stock items include bolts, guides, pilot pins, punch heads, retainers, screws and springs.
For a list of standard size punches, see below.*
There is a 20% restocking fee for stock items and standard size punches.
Products must be returned in new condition within 30 days of receipt for refund. Return shipping is not included. Refunds are for the cost of the products only.
Please email us at info@unittool.com to receive a Return Merchandize Authorization number.
Custom sized items are non-refundable.
For orders cancelled within 24 hours, there is no restocking fee for stock items.
For orders cancelled after 24 hours, the return policy above applies.
.1250 |
.1406 |
.1562 |
.1875 |
.1960 |
.2020 |
.2031 |
.2187 |
.2500 |
.2570 |
.2600 |
.2656 |
.2812 |
.3125 |
.3437 |
.3750 |
.3906 |
.4062 |
.4375 |
.5000 |
.5312 |
.5625 |
.6250 |
.6875 |
.7500 |
.8125 |
.8750 |